The 12 Pillars of LEAN Manufacturing.
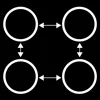
1. Cellular Manufacturing
Cellular manufacturing is based on arranging equipment and workstations based on a group of different processes located in close proximity to manufacture a group of similar products. This arrangement reduces cycle time and inventories to meet market response times.
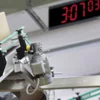
2. Takt Time
Takt time is the average rate at which a company must produce a product or execute transactions based on the customer’s requirements and available working time.
Takt Time Formula
T = Ta/D
T=Takt time, e.g. [work time between two consecutive units]
Ta=Net time available to work, e.g. [work time per period]
D=Demand (customer demand), e.g. [units required per period]
Net available time is the amount of time available for work to be done. This excludes break times and any expected stoppage time.
Using a Digital Timer System can help establish and maintain the amount of time required for production.
A process of documenting description of methods, materials, tools, and processing times required to meet Takt Time for any given job. This aids in standardizing the tasks throughout the value stream.
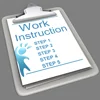
3. Standardized Work
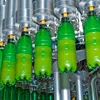
4. One Piece Flow or Continuous Flow
This concept emphasizes reducing batch size to eliminate system constraints. A methodology by which a product is produced by moving at a consistent pace from one value-added processing step to the next with no delay in between.
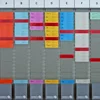
5. Pull Systems and Kanban
Wherein a customer process signals a supply process to produce or deliver a product when it is needed. Kanban is the signal used within a pull system through scheduling combined with travelling instruction using simple visual devices such as cards or containers.
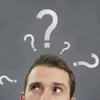
6. Five Why's
A thought process by which the question “why” is asked repeatedly to get to the root cause of a problem.
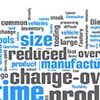
7. Quick Changeover / SMED
A 3-stage methodology developed by Shigeo Shingo that reduces the time to changeover a machine by externalizing and streamlining steps. Shorter changeover times are used to reduce batch sizes and produce just-in-time. This concept aids in reducing the setup time to improve flexibility and responsiveness to customer changes.
Using a Digital Timer System can help establish and maintain Changeover goals.
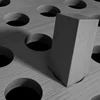
8. Mistake Proofing / Poka Yoke
A methodology that prevents an operator from making an error by incorporating preventative built-in responsiveness within the design of product or production processes.
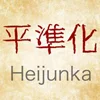
9. Heijunka / Leveling the Workload
A methodology that prevents an operator from making an error by incorporating preventative built-in responsiveness within the design of product or production processes.
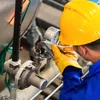
10. Total Productive Maintenance (TPM)
A team-based system for improving Overall Equipment Effectiveness (OEE), which includes availability, performance and quality. This aids in establishing a strategy for creating autonomous employee ownership for equipment maintenance. The goal of the TPM program is to markedly increase production while at the same time increase employee morale and job satisfaction.
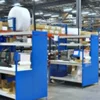
11. 5S
5S is a five step program aimed at creating and maintaining an organized visual workplace.
SORT
Separate those things needed for the job from those not needed. Examples include obsolete and expired procedures, damaged and expired inventory, defunct/old equipment. At the end sort, unneeded items are disposed of.
SET IN ORDER
For things needed to do the job, put them in a logical order or logical placement to enhance the work process and reduce the chance of defects. The order should contribute to the reduction in excess movement, excess transportation, over processing, over production, excess inventory, excess delays and defects. These are the 7 wastes LEAN methods eliminate in an organization.
SHINE
The work area is cleaned and equipment and systems are calibrated to optimal settings such that the process is in its ideal state. At this point, measurement of the system may begin and the measurements will capture the variation of the process rather than that of the environment or the measurement system. This allows better understanding of process variation.
STANDARDIZE
While there may be “many ways” to do the work, there is “one best way” to do the work. Collaboration with those in the work place and with process engineers can identify the best way to achieve the work. This should become the standard. This includes how to do the work and how to replenish the work such as thresholds and manage inventory.
SYSTEMATIZE
Put into place the system to maintain the organization of the workplace, the upkeep of the equipment and system and the measurement, monitoring and visual control of the process. Visual control allows everyone to understand how the process is performing. This implies a “feedback and response” mechanism enabling the individual to exercise control and accountability for his/her work.
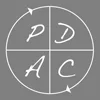
12. Problem Solving / PDCA
The PDCA cycle is a graphic representation of how most individuals have already solved problems. This system is used for identifying and solving problems at their root cause and then implementing counter measures with monitoring.
PLAN
Establish a plan to achieve a goal.
DO
Enact the plan.
CHECK
Measure and analyze results.
ACT
Implement necessary reforms if results are not as expected.
-
S9D2R6CALS LED Digital Timer, Red, 2.5″ Numeral, 6 Digit, Silver, 105-240V AC
Measure elapsed or remaining time during critical events.
- Counts up (elapsed time) or counts down (time remaining)
- Use in conjunction with TimeTrax Sync™ Digital Timer Controller (sold separately)
- Large, 2.5″ high 7-segment numerals
- Ultra bright red LED digits (up to 150′ viewing distance)
- Hour:minute:second, 6 digit display (00:00:00)
- Displays negative symbol and flashes when counting down past zero
- 105-240V AC 50/60Hz
- Made in USA
Requires TimeTrax Sync™ Digital Timer Count Up/Countdown or Code Blue Controller (sold separately).
$473.00 Shop Now -
S9D4R6CALB LED Digital Timer, Red, 4″ Numeral, 6 Digit, Black, 105-240V AC
Measure elapsed or remaining time during critical events.
- Counts up (elapsed time) or counts down (time remaining)
- Use in conjunction with TimeTrax Sync™ Digital Timer Controller (sold separately)
- Large, 4″ high 7-segment numerals
- Ultra bright red LED digits (up to 250′ viewing distance)
- Hour:minute:second, 6 digit display (00:00:00)
- Displays negative symbol and flashes when counting down past zero
- 105-240V AC 50/60Hz
- Made in USA
Requires TimeTrax Sync™ Digital Timer Count Up/Countdown or Code Blue Controller (sold separately).
$529.00 Shop Now